When bidding a large contract to perform live line maintenance along 12,000 kilometers (nearly 7,500 miles) of transmission lines in Kuwait, High Line Division S.L. was faced with an important challenge — how to access the lines safely and cost efficiently. Options were limited, due to the height of the towers, local laws and other factors. In the end, the use of a new, cost-effective insulated work platform proved key to bidding the project competitively while keeping profitability within reach.
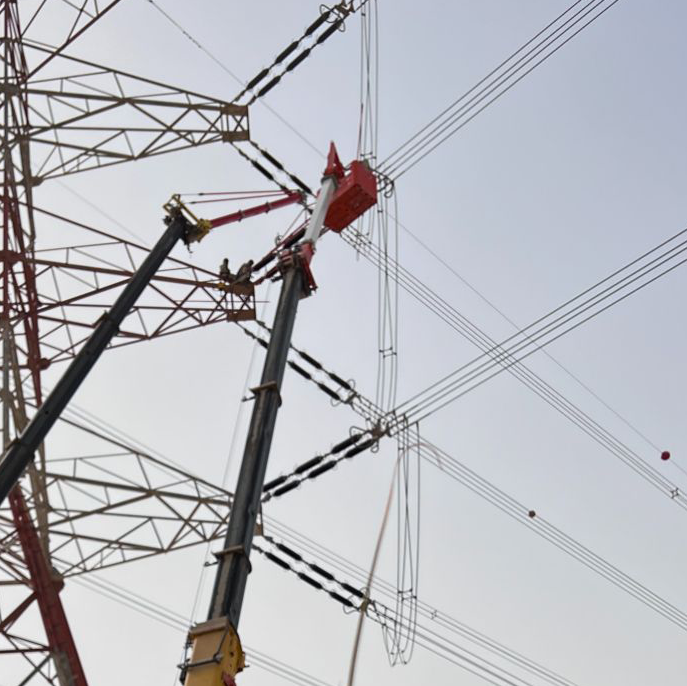
Formed in 2004, High Line Division was originally created to provide live line maintenance to the oil and gas sector in Libya. After operations there were discontinued in 2012, the contractor registered in other countries, successfully completing projects in Spain, Chile, Indonesia, Maroc, Yemen, Saudi Arabia and more.
One of High Line Division’s core services is the application of room temperature vulcanizing high voltage insulator coating (RTV HVIC). This process, which can be used on electrical substations as well as overhead transmission and distribution lines, was an ideal solution for Kuwait’s environmental challenges.
Despite being oversized, the transmission insulators used in Kuwait require frequent washing — three or four times per year — due to high levels of pollution. The washing became very expensive, especially considering that the towers range from 60 to 80 meters (197 to 262 feet) in height, which contributed to the cost.
To address this issue, High Line Division proposed RTV HVIC coating for the insulators, which would help protect them against pollution. With the coating the insulators could last up to 10 years without undergoing maintenance, resulting in significant cost savings.
High Line Division’s bid included barehand work with 132 kV, 300 kV and 400 kV voltages. Unfortunately, the contractor struggled finding solutions for its linemen to access the insulators at competitive costs. Hand climbing the towers is not legal in Kuwait, largely due to extreme temperatures well over 100 degrees Fahrenheit. Additionally, the only insulated lift options available to access the tall towers were too expensive to complete the work within budget.
“Due to the height of these towers, there are no bucket trucks that will reach the insulators,” said Daniel Granja Pardiñas, Chief Executive Officer for High Line Division. “Insulated aerial lifts cost over $1 million, and that would not allow us to compete for the project financially. But, after extensive research, we discovered cost-effective insulated work platforms that would work on standard cranes.”
The insulated work platforms Pardiñas found were developed by LineWise. Designed to do the work of a Category A insulated aerial lift at a fraction of the price, the insulated work platforms attach to standard cranes, making the equipment compatible for high-voltage barehand maintenance up to 765 kV.
When awarded the contract, High Line Division purchased six insulated work platforms, as well as six insulated masts, which also attached to cranes for lifting energized lines. Additionally, the contractor purchased 12 cranes dedicated for use with the insulated work platforms and masts.
Another advantage of using cranes instead of specialized insulated lifts for the contract is the ability to sell them after the project is completed. “When we’re finished with the cranes, it’s very easy to sell them and recover the investment,” said Pardiñas. “It’s not easy to sell the more expensive insulated lifts, even in the Middle East. This factor helped make our cost competitive.”
After completing LineWise’s training on the new insulated work platforms in the U.S., High Line Division began the RTV HVIC coating process, and the cranes performed as hoped. The hydraulic articulation feature on the insulated work platforms especially helped increase safety and productivity for the linemen. This articulation was controlled by operators on the platforms via radio remotes.
“When you work in live line, the position in which your body has to perform the job is very important,” said Pardiñas. “The ability of the platform to turn, rotate and approach the insulators is what made us decide to use the LineWise solution.”
In addition to controlling the position of the insulated work platforms with remotes, High Line Division worked with the crane manufacturer to develop remote controls for the crane functions. “A simple hanging basket would not allow us to do the work as effectively,” said Pardiñas. “The more hydraulic movement capabilities we have reduces the chances of an incident when working with 400 kV live lines. All of this is a value added for us.”
The vast majority of the RTV HVIC coating work has been completed, and High Line Division looks to replicate the process elsewhere, due to the success in Kuwait. The contractor is currently preparing for another large project in Africa, where it plans to deploy a similar system using locally sourced cranes.
“We achieved a way to work with any crane, anywhere,” said Pardiñas. “Imagine having to work at extreme heights in another corner of the world. You cannot move a complete crane, but for us it’s very simple. We just ship one container with the insulated solutions inside, purchase a crane where it’s needed, make the assembly, and we are done.”
Of course, each country has its own regulations on which methods can be used. But for the U.S., Middle Eastern and African countries at least, the insulated work platforms seem to provide an ideal solution for bidding contracts competitively and completing live line maintenance safely. According to Pardiñas, “We’ve figured it out!”
Leave a Reply